For ages, we have referred to the process of preparing art for the press as prepress. However, as automation has played a major role in the process of printing, so has the role of prepress. We should acknowledge that prepress extends far beyond the press itself.
Prepress has been defined as the function where data (what to print and how) and the asset (how it is supposed to look; the graphics) come together. Prepress tools need to be open and flexible to ensure that communication exists from the origin of data (often MIS/ERP) to the equipment required to make the plate and print the asset. It means communication ties must exist between:
- MIS/ERP
- Color Management/Conversion
- Plate Making/Plate Cutting
- Mounting & Application of Tape
- The Press
- Inspection—Including Color
- Slitting Areas
Achieving Automation
Automation is the operation of a process by mechanical or electronic devices that take the place of human labor. Although we would like to consider ourselves infallible, humans can break automation. Yet, we are necessary for logical decisions. Our ultimate goal for automation is to combine the good and the bad: reduce human touches, human interaction and the duplication of tasks creating greatest efficiencies.
Prepress works with precision; for example, a measurement value of points, which is 1/72 of an inch. But, while it has gotten closer over the years, the flexo plate making process is still not exact. While this is a challenge the industry is aware of, there still are requirements to compensate for some inaccuracies.
Design tools have been used to conduct prepress tasks for many years, but they are creative tools. They are built to design something from nothing; not to create many from one and repeat the same process over time. This is where prepress comes in. It takes these files and provides the manufacturing expertise to build them for the print floor.
Prepress needs to focus on manufacturing efficiencies. These include:
• PDF Processing Steps for Packaging: The best packaging workflows are going to be, of course, those that focus solely on packaging. Not only do they tend to follow a more traditional packaging workflow; they also tend to have greater packaging ties to CIP4 standards. Packaging workflows are in tune with all new packaging technology changes
• Familiar Terms for Manufacturing: Packaging prepress tools are more sensitive to very specific needs, such as not relying on inks and layers that can be destroyed. They are also programmed to be specific to packaging nuances such as special color management, three dimensions and folds, use of spot varnishes and white ink layers, etc
• Enabling Better Automation for Packaging: Building systems from preflighting to press inspection allows prepress experts to focus on the more challenging issues. The more standardization that can be built for an automated prepress system, the more efficiently, and quickly, it will operate
• Embracing Standards Technology Leads to Greater Automation: This not only comes in play with PDF, XML and JDF files, but more specialized files, such as Collada
Typically all of the necessary information to manufacture a job for a lot of packaging—most notably flexible packaging—doesn’t exist in any “off-the-shelf” system. There are just too many variables that are usually much more complex than what you would find in a traditional commercial print assignment.
Data & Details
MIS/ERP systems used for manufacturing a product rarely offer an exact description of the data required to produce the packaging job with the desired look. Thus, developers of advanced prepress tools need to be able to gather these details from other systems or be able to store this information themselves for use on repetitive manufacturing.
To make this even more nuanced, the prepress application needs to understand the specifics of each press in the plant. So, data that is stored is also typically associated with a specific press specification.
Experienced packaging prepress departments are familiar with the many tasks that are required from a prepress workflow application. They can include:
- Understanding the Inks and the Ink Order: Special inks, of course, have been a common trait of package printing for years. While expanded gamut printing can make this process more standardized, it still requires an understanding of how far a brand color deviates from its traditional representation
- Color Management: The more a prepress workflow can automate the control of color ultimately on press, the easier the package printer’s job will be
- Trapping: Flexo presses are more accurate than ever, and make-readies are much faster. However, automated trapping settings for each press are desired
- Step and Repeat: This is where a good prepress system can automate the step and repeat process and automatically create the most optimized and cost-efficient solution
- Bearer Bars: A good workflow—or one that communicates well with a good color management system—can help define the specs of each job’s bearer bars, helping the flexo press read the impression and maintain as minimal bounce as possible
- Microdots: Many workflows contain RIPs to drive the flexo plate imager. Many now enhance the quality of a halftone by including microdots to best represent highlights. It turns out that it’s best to use microdots when the job doesn’t contain surface screening, for most accurate mounting. Highly magnified cameras are reading these dots in the specified areas, so it is best to have full and complete dots.
- Other Required Plate Identifiers for Plate Manufacturing: We want to make sure that the correct plates are mounted onto the press. This could include specialized data matrix codes or other item numbers to mark and identify the plates
Talk to Me
A good system will have worked out an ability to communicate among its prepress tools to achieve acceptable efficiencies.
Different functional portions of a prepress system can communicate and work together to achieve reasonably complex goals. For example, a system could:
- Create cut lines, unique to the separation for optimal flexo plate usage, to stagger plates delivered for cutting
- Determine the height and width of the plate and send that information to an automated tape applicator. At the same time, that data is returned to the MIS/ERP system for costing
- Establish the location of the microdots in association to the plate, for precise mounting
- Determine the ink order for the proper loading of cylinders on press to match what color management had specified
Automated prepress systems permit staggered cutting areas to be applied to shrink sleeve label designs, like the one depicted here.
Once all the prepress manufacturing data is gathered, it needs to be assembled and delivered upon a “trigger.” A data “trigger” could be as simple as entering a unique item number. Perhaps the barcode scan from a system can include this unique identifier.
There could be a status change in the data system (typically delivered by the MIS/ERP). Once the trigger has been initiated, a solution should deliver to the system, in the requested format. This could be XML metadata, an API door to the system, CSV file format data, a database action, or a properly formatted PDF file.
What data is delivered between systems? Certainly, it would include details about how the asset was prepared. It will also include information about the pressrun.
Of course, data about step-and-repeat is delivered. That would include the number of pieces of art across and down, as well as the size of gaps. This is critical for inspection, and the gaps are important details to send to the slitter.
Packzimizer intelligently analyzes the order data to optimize the layout and repetitions of labels on the roll based on quantity, offering maximum substrate usage and press uptime.
Then, there’s the role of prepress on the press, for inspection. Any inspection tool needs to know what to inspect for. It could be content, or areas within content, removing any necessary irrelevant processing steps, such as dielines, varnishing, or other print features. Prepress also plays in important role defining where—and what—to inspect for color matches. Quantities are imported from the MIS/ERP to the prepress automation system, as well as the inspection system.
PACKZ 10 to deliver supreme quality and detailed printing on metal cans. HYBRID Software’s Capture 3D Technology now features precise deformation grids and live 3D viewing, unlocking new opportunities for branding and metal can packaging.
It also needs to validate the barcode against product data during a production run. Lest we all forget, this is how we all get paid, from the brand to the printer!
Critical Communication
Whether the printing model for a certain package runs through a trade shop (often the case for flexible packaging) or by a converter with a complete in-house plate making capability, there are still requirements for automated communication between prepress and the plate making department, including chosen systems for mounting, tape application, inspection and any post flexo plate making needs, which shouldn’t hinder efforts to achieve precise automation.
Flexo plates are expensive. When producing a corrugated box, often only a tiny area is printed, even though the plates, themselves, may be large. In the past, a great deal of manual work was required to avoid imaging large flexo plates with very few graphics. A good prepress system automatically can separate printed elements in the design file and consolidate and optimize them to take up the least amount of plate space, minimizing material use.
If done right, it can be associated within a pure PDF workflow and tie into the MIS/ERP. For example, job specs including polymer, thickness, and sizes, among other variables, can be embedded into the mounter’s XML file (both PDF and TIFF/LEN files). An automated system like this can save 5-10 or more minutes to patch an entire job, and with fewer errors. Printers have reported 50 percent prepress savings.
Even more sophisticated systems can include scrap and cutoff inventory management of flexo plates. They identify and tell plate imaging operators which cutoffs could be used for a job, and how to use them, utilizing what could have gone bad on the shelf, invisible to the plate maker.
Where to Begin
According to Automation Advantage, published by McGraw Hill, automation is a journey. It begins with a vision of what you want to achieve. To make it reality, we must be aware of what our system is today—what we’re doing—and what systems and processes need to be put in place to reach our automation goal. It’s about creating a baseline of where you are and where you’d like to end up.
While creating your prepress automation roadmap, you should also create your operation’s own roadmap for this major project. It includes determining what opportunities exist by automating, creating business and key performance indicator mapping, and a blueprint/plan.
You get the automated system live by first testing it offline, assuring that the process works, and the platform you are using is ample for your objectives. Seeking the help of industry and technology wide accelerators and standards also helps.
As it is implemented, the automation journey will require oversight and governance to make sure you are on the right track.
Finally, you need to communicate the changes to the organization. Often, this is the most complex step; the one that delivers the most trials and tribulations. Often, the project manager will get many others involved in the installation project, so they have some ownership.
Even after you think your job is over, it isn’t. There are always continuing revisions and updates. Partnering with the correct industry suppliers is important to meet any vision of an optimized, automated prepress system. Remember you are planning for the future—not investing in the past.
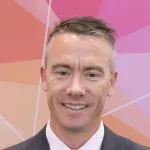
About the Author: Mike Agness is executive vice president, Hybrid Software, Americas. The firm delivers innovative prepress software solutions to various packaging-related businesses. Hybrid’s software tools are flexible, open, built on industry standards and have proven to provide significant efficiencies to the packaging industry. Hybrid Software Group is comprised of Hybrid Software, Global Graphics (Harlequin RIP), Meteor Inkjet, Xitron and ColorLogic GmbH.